SERVICE
What is MIM?
Metal powder injection moulding (MIM) is a manufacturing method for metal products by injection moulding material called feedstock, which is a mixture of metal powder and a binder made of resin, wax, etc., into a mould and sintering them.
MIM process
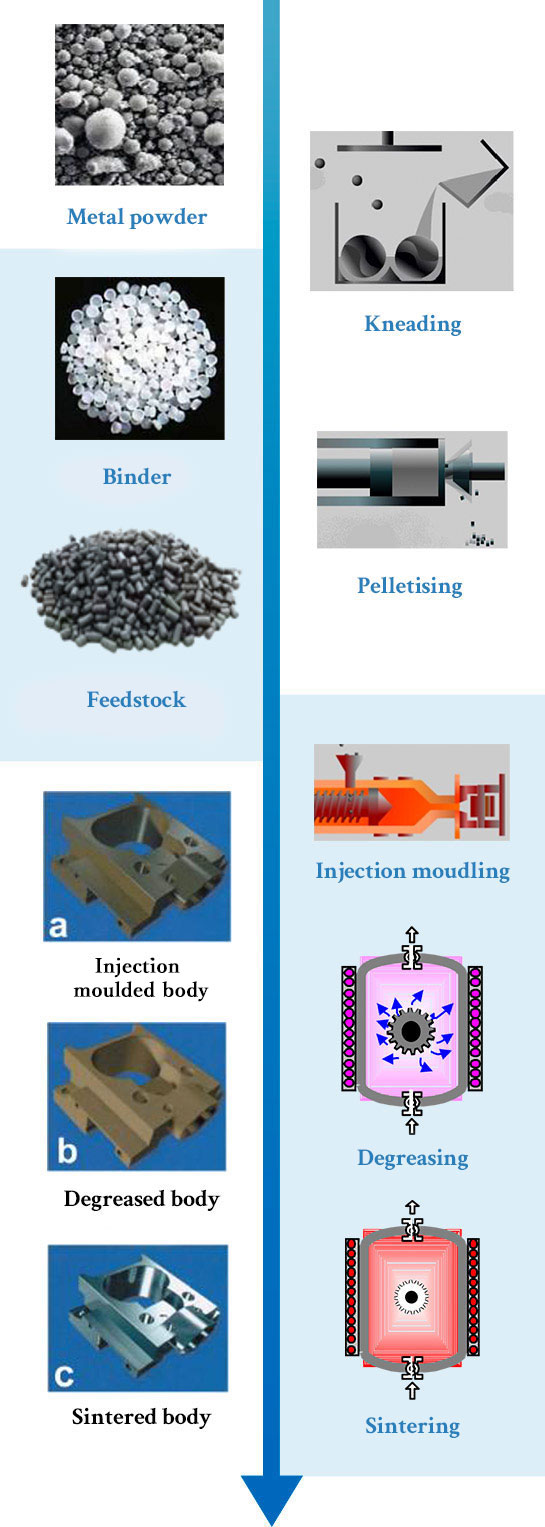
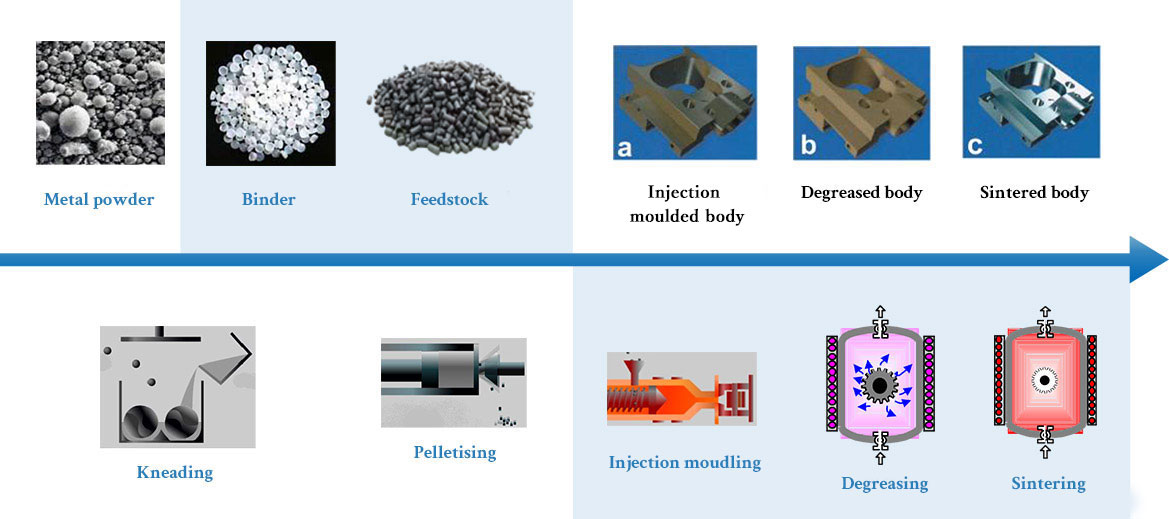
MIM Features
Conventional MIM | Additional feature by μ-MIM® | |
---|---|---|
Material |
|
|
Design |
|
|
Injection moulding |
|
![]() |
Sintered body |
|
|
Accuracy and specifications
Conventional MIM | μ-MIM® | ||
---|---|---|---|
Material | Length | <50mm |
<10mm Maximum 30mm in one direction |
Thickness | 0.5~5mm | ||
Minimum wall thickness | 0.3mm(partial) | 0.1 mm (6mm square) | |
Smallest hole size | 0.3mm(partial) | Φ0.03mm | |
Tolerance | < 5mm | +/- 0.03mm | +/- 0.01mm |
5-10mm | +/- 0.04mm | +/- 0.03mm | |
10-20mm | +/- 0.08mm | ||
20-30mm | +/- 0.15mm | ||
Relative density(%) | 95-98 | > 98.5 | |
Surface roughness (Ra) | < 3μm | 0.3μm(In case of applying ultra fine powder) | |
Rmax | < 10μm | 2~10μm | |
Product weight | < 50g | ≦ 10g |
What is μ-MIM®?
μ-MIM® is a technology that realises ultra-precise MIM components. It is a technology that includes not only miniaturization of the product size but also its accuracy and quality assurance.
μ-MIM® meets the following demands.
- ▪ Mass production of components and materials that are difficult to machine
- ▪ Integration of small components that are difficult to assemble
- ▪ Mass production of components with size and tolerance requirements that are difficult by conventional MIM production
- ▪ Add value to components by integrating functions
In conventional MIM, most of the parts have a size of several millimetres to several centimetres and must satisfy the dimensional tolerance of
about 5-10% of its size.
The product size is smaller, the required tolerance is also smaller thus the difficulties of manufacturing is increased.
μ‐MIM® realises mass production in that area
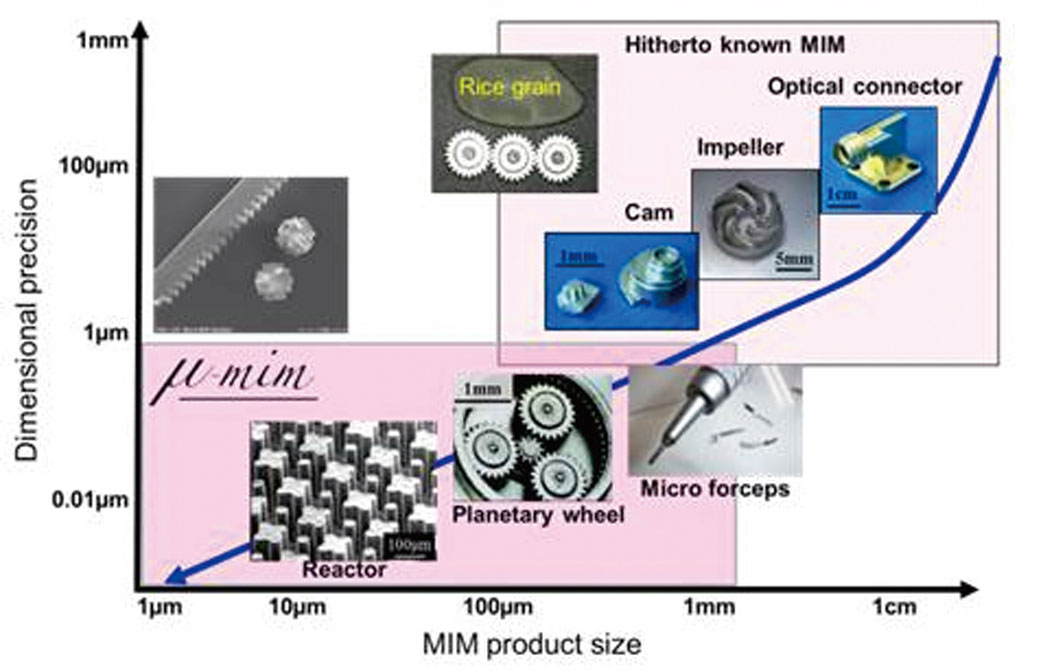