SERVICE
μ-MIM® fundamental technologies
Manufacturing technology

Evaluation technology
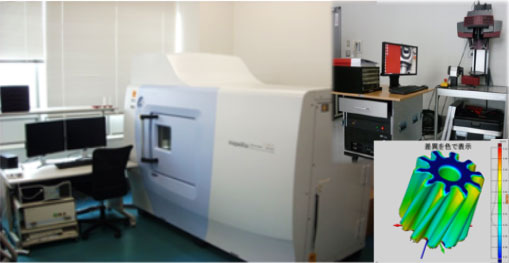
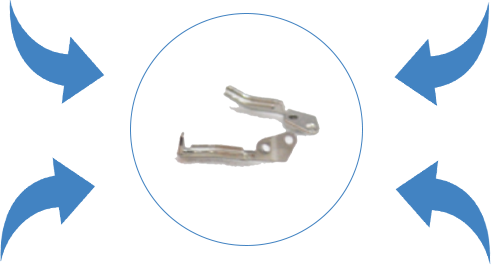
Material technology
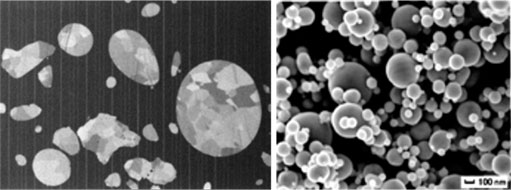
Analysis technology
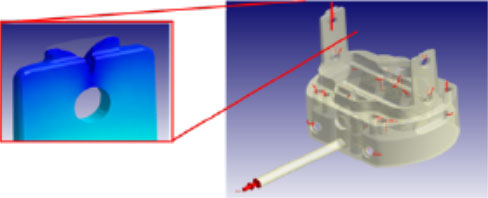
Original binder system
The most important factor in realising ultra-high precision MIM (metal injection moulding) is our original binder system. In the first step of MIM production, metal powder is kneaded with a binder made of resin mixture to pelletized feedstock, the material of MIM.
We determine the optimal proportion between metal powder and binder for every material type. The binder compatibility depends on the metal type, powder shape and size. Thus, the viscosity of feedstock and the binder decomposition reaction during the degreasing process will be different as well. These differences affect the final component quality significantly. Therefore, the binder type and mixing ratio are determined for each type of MIM component.
Since Taisei Kogyo Co., Ltd. uses its originally developed binder system, it is possible to produce highly precise and complex designed MIM components in large quantities.
MIM manufacturing technology using a fine powder
MIM components are sintered metal powder with high density, and the as-sintered surface is usually matt (crepe or so-called pear-skin surface). If required, the mirror finish is available. In addition, the parting lines, gate marks and ejector pin marks appear on the surface. Therefore, when MIM is applied for exterior parts, you may need to add extra processes such as polishing.
To address this issue, Taisei Kogyo Co., Ltd. has developed a MIM manufacturing technology using finer metal powder. The use of finer metal powder increases the manufacturing difficulty and material price. However, it enables a smooth surface as shown below. Not only the surface roughness can be improved, but also the parting lines can be reduced to an invisible level that does not affect the appearance. Our technology realises exterior parts and functional components for serial production.
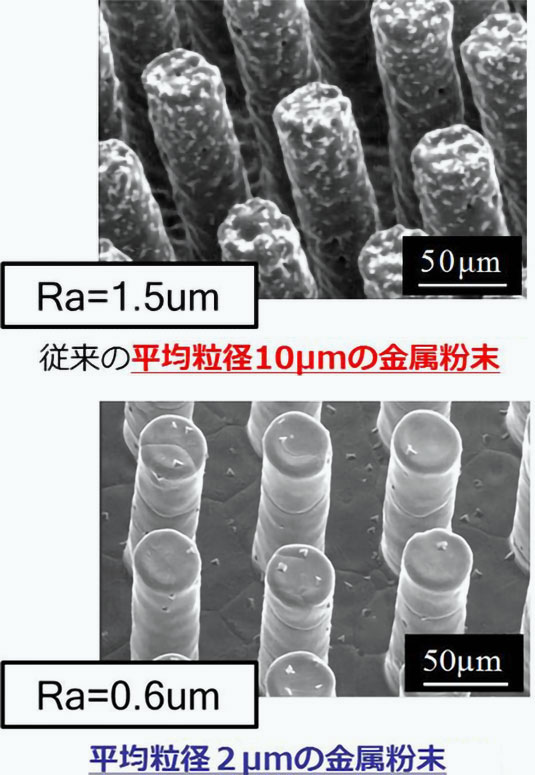
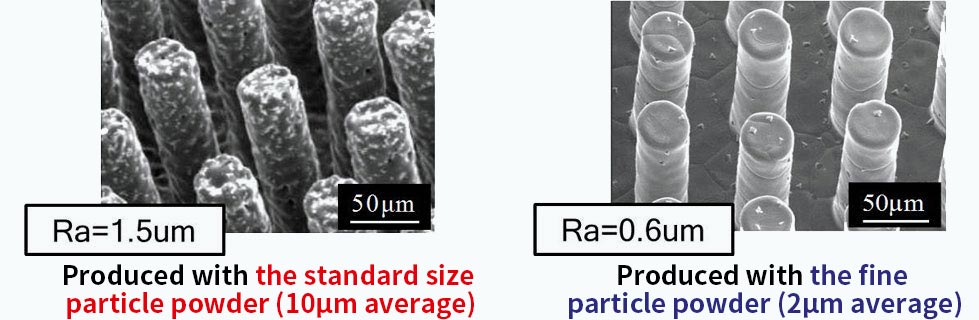
Reliable mould process
An ultra-precise design and tooling are realised thanks to many years of experience in precision injection moulding of metal parts
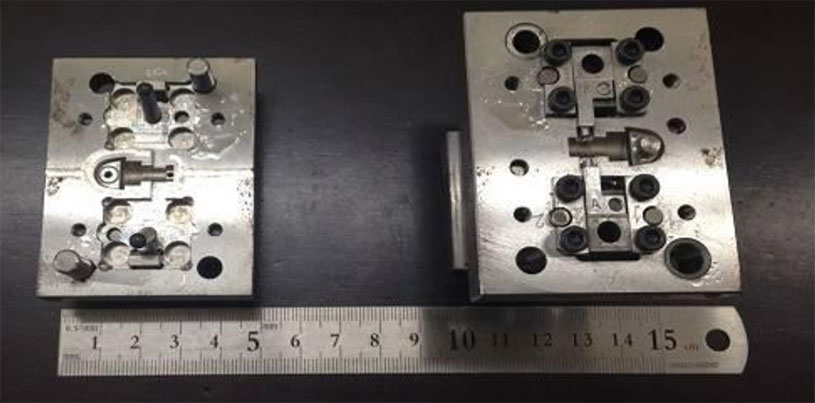
Possible defects during the moulding and sintering process are also examined from the mould design stage. Therefore, the gate design needs to be planned carefully, even more than plastic injection moulding. Jetting might happen in the plastic moulding, but the cause and the result due to jetting in the MIM process differ from that of the plastic injection moulding. In the case of MIM, the specific gravity between the metal powder and the binder is greatly different. Thus, metal powders move in the mould, often causing jetting due to the law of inertia. The phenomenon makes the distribution of the metal powder heterogeneous, which might result in defects and poor quality of the sintered components such as a crack. Taisei Kogyo Co., Ltd. has jointly developed and deploys injection moulding analysis software specifically for our MIM process.
A slight difference in gate arrangement of moulds for micro components directly leads to possible issues such as moulding defects, yield rate decline, eventually cost increase in mass production.
In our μ-MIM® production, these problems are minimised through in-depth simulation and our MIM moulding experiences, so that the other MIM manufacturer cannot compete with us.
State-of-the-art degreasing and sintering technology
In general, a MIM production process deploys the binder degreasing of the moulded bodies by solvent to avoid distortion and damage through thermal degreasing just after the injection moulding process. However, organic solvents are regarded as harmful for humans as well as for and the global environment. Furthermore, the degreasing process by organic solvent takes a long time.
Taisei Kogyo Co., Ltd. uses an originally developed binder system, which will be decomposed completely during the thermal degreasing process and does not affect the quality of sintered components negatively. Our binder system enables effective production with this binder system which is decomposed during the debinding and sintering phase completely through an one-step furnace.
For these processes, several points are taken into consideration, e.g) densifying the components, avoiding dimensional deviation after sintering, contamination of carbide or oxidation of components. Especially, the bigger its specific surface area is, the more the reactivity of ultra-fine metal powder applied for μ-MIM components becomes increased. It leads them to be more sensitive against the slight change of sintering conditions, in particular temperature uniformity and atmosphere control. At the μ-MIM sintering step, tens of thousands of components are put into the furnace and these conditions exert influence on temperature distribution there as well as reproducibility between batches, eventually on the process capability index of each lot. Therefore, optimizing these conditions according to the components character is significantly important.
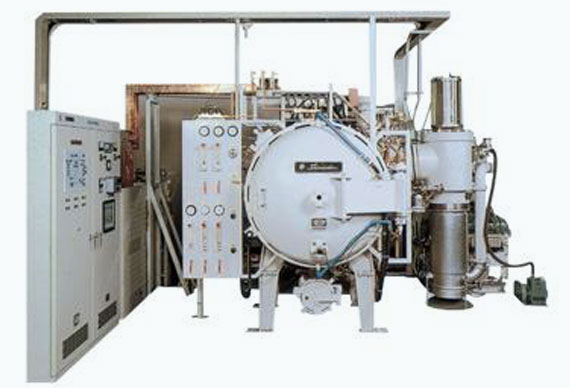